航天產(chǎn)品精益總裝生產(chǎn)系統(tǒng)仿真優(yōu)化應(yīng)用介紹
發(fā)布于:2021-06-17 來源:大禹匯智
項(xiàng)目背景
航天產(chǎn)品的裝配是實(shí)現(xiàn)產(chǎn)品功能的重要階段,也是產(chǎn)品質(zhì)量特性形成的關(guān)鍵環(huán)節(jié)。現(xiàn)代航天產(chǎn)品配置的系統(tǒng)設(shè)備多、安裝布局復(fù)雜,質(zhì)量標(biāo)準(zhǔn)和安全標(biāo)準(zhǔn)要求高,進(jìn)而造成傳統(tǒng)裝配工藝改進(jìn)較為困難。另外,在廠房設(shè)計(jì)規(guī)劃之初,傳統(tǒng)的二維呈現(xiàn)在理解的直觀性方面存在天然缺陷,使得很多工藝流程、裝配過程、檢測過程、物流路徑等存在的問題直到實(shí)際生產(chǎn)時(shí)才被發(fā)現(xiàn),很容易造成巨大損失。
經(jīng)過近幾十年的發(fā)展,為了更好的解決上述問題,我國航空航天工業(yè)開始將精益制造理念、計(jì)算機(jī)輔助工程方法和信息化技術(shù)集成在一起進(jìn)行工藝流程設(shè)計(jì)、廠房精益布局來滿足不斷上升的產(chǎn)能需求與及時(shí)交付要求。
項(xiàng)目目的
針對航天科技集團(tuán)XX廠總裝車間智能產(chǎn)線建設(shè)目前所面臨的問題,對已有的裝配工藝流程、物流存儲系統(tǒng)進(jìn)行科學(xué)的分析和評估,用分析方法和具體數(shù)據(jù)來找到現(xiàn)有裝配工藝流程和總裝生產(chǎn)系統(tǒng)中的瓶頸。
對總裝裝配線生產(chǎn)系統(tǒng)內(nèi)各變量,如生產(chǎn)效率、工作量、庫存、停工、故障、質(zhì)量等因素進(jìn)行離散事件建模,來進(jìn)行工藝流程仿真、物流系統(tǒng)規(guī)劃分析,以實(shí)現(xiàn)數(shù)字化裝配線設(shè)計(jì)。
用仿真分析的方法,評估這些參數(shù)變化對生產(chǎn)系統(tǒng)性能的影響,實(shí)現(xiàn)對現(xiàn)有生產(chǎn)線瓶頸的分析和優(yōu)化,實(shí)現(xiàn)生產(chǎn)線工藝規(guī)劃和工藝布局設(shè)計(jì)驗(yàn)證。對迭代設(shè)計(jì)的工藝平面布局進(jìn)行合理性分析,在現(xiàn)有物理設(shè)備基礎(chǔ)上,結(jié)合工藝流程、物流順暢性、生產(chǎn)能力等因素給出當(dāng)前各功能區(qū)域布局優(yōu)劣性的評估。
解決方案
基于成熟的商業(yè)化離散事件仿真工具Witness,針對航天XX廠未來總裝車間涉及的9種產(chǎn)品的生產(chǎn)流程建模,以當(dāng)前的廠房布局為基礎(chǔ),以當(dāng)前工房內(nèi)部的加工設(shè)備性能參數(shù)為主要條件建立起整體的生產(chǎn)模型,包含廠房內(nèi)部所有的生產(chǎn)加工資源和人工配備。通過動態(tài)的流程仿真,評估系統(tǒng)的有效生產(chǎn)能力,識別流程瓶頸并給出優(yōu)化的管理和改進(jìn)建議。
在本項(xiàng)目實(shí)施過程中建立的仿真模型具備如下功能:
? 仿真模型可以輸出車間內(nèi)部所有緩存區(qū)的狀態(tài)統(tǒng)計(jì);
? 仿真模型可以輸出車間內(nèi)部所有加工資源(設(shè)備、工人)的利用率與狀態(tài)統(tǒng)計(jì);
? 仿真模型可以輸出車間內(nèi)部所有加工工人的繁忙率與狀態(tài)統(tǒng)計(jì);
? 仿真模型可以輸出所有物流節(jié)點(diǎn)與路徑的物流量信息;
? 仿真模型可以輸出所有產(chǎn)品的加工周期;
? 仿真模型可以針對具體的生產(chǎn)計(jì)劃,評估所有產(chǎn)品的及時(shí)交付情況。
根據(jù)模型輸出的以上幾大類結(jié)果數(shù)據(jù),結(jié)合成熟的數(shù)據(jù)分析技術(shù)即可以計(jì)算出諸如單機(jī)效率、人工效率、有效產(chǎn)能等表征生產(chǎn)線性能的評價(jià)指標(biāo)。進(jìn)一步依據(jù)這些主要評價(jià)指標(biāo)指導(dǎo)后續(xù)生產(chǎn)線的優(yōu)化方向,評價(jià)預(yù)期的優(yōu)化手段是否有效。
圖1 仿真模型執(zhí)行步驟
圖2 投料邏輯流程圖
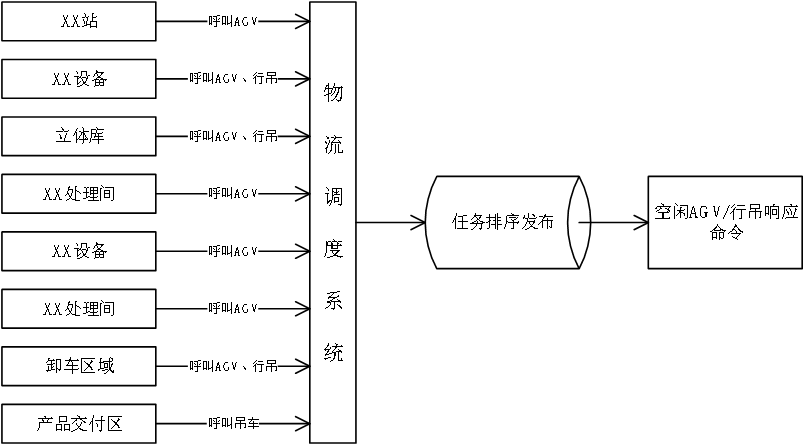
圖3 物流任務(wù)調(diào)度結(jié)構(gòu)
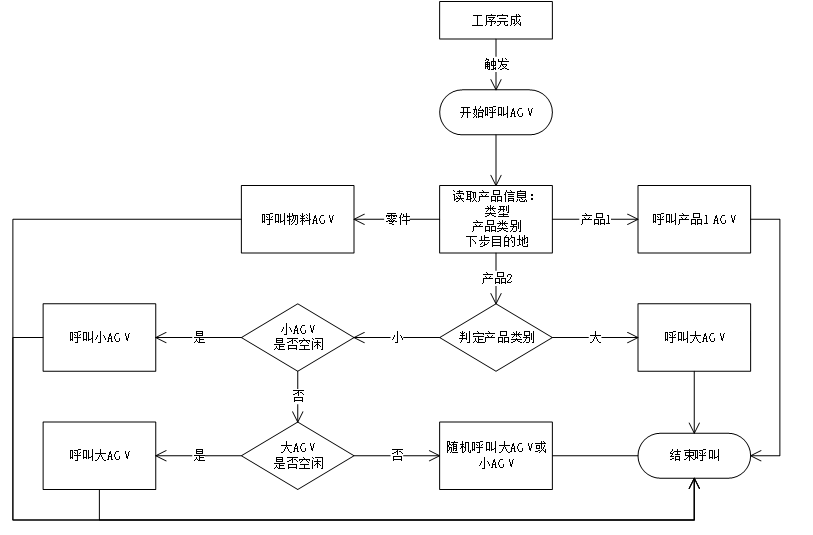
圖4 AGV呼叫邏輯圖
項(xiàng)目成果
項(xiàng)目建立了可以反映航天XX廠未來總裝車間的運(yùn)行仿真模型,通過仿真運(yùn)行的模型,能夠得到廠房內(nèi)部所有生產(chǎn)資源的仿真結(jié)果,為后續(xù)廠房的優(yōu)化提供方向與建議。
圖5 各產(chǎn)品加工時(shí)間箱線圖
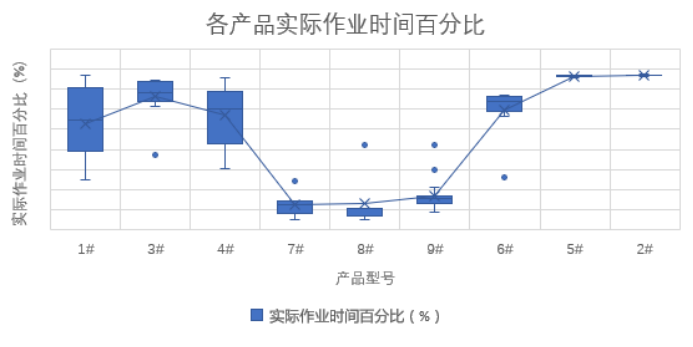
圖6 各產(chǎn)品實(shí)際作業(yè)時(shí)間半分比箱線圖
圖7 AGV狀態(tài)統(tǒng)計(jì)
圖8 設(shè)備狀態(tài)時(shí)間百分比統(tǒng)計(jì)
根據(jù)上述的結(jié)論,在仿真中進(jìn)行了相應(yīng)的優(yōu)化迭代,主要針對XX環(huán)節(jié)。在仿真中設(shè)計(jì)了“效率系數(shù)”參數(shù),以效率系數(shù)的變化來表征XX效率的提升,如效率系數(shù)為0.9,則表示提升后的工序加工時(shí)間為當(dāng)前加工時(shí)間的90%,通過仿真得到了如下的結(jié)論。
總結(jié)
在本項(xiàng)目中,基于Witness仿真軟件,根據(jù)未來總裝廠房的規(guī)劃,建立了生產(chǎn)仿真模型。通過仿真模型的運(yùn)行得出了未來總裝廠房運(yùn)行各方面的統(tǒng)計(jì)結(jié)果。以最初的初始廠房布局與工藝流程為基礎(chǔ),經(jīng)過工藝的改進(jìn)與布局的調(diào)整,通過迭代仿真最終達(dá)到了設(shè)計(jì)目標(biāo)。在此過程中給出了物流設(shè)備的配置方案,給出了立體庫設(shè)計(jì)的容量要求,給出了廠房緩存區(qū)的面積要求,給出了工人工作量的分配方案。
綜上所述,通過Witness仿真建模的方法,能夠高效、直觀、定量地對設(shè)計(jì)方案進(jìn)行評估,為設(shè)計(jì)方案的改進(jìn)提供方向性的指導(dǎo)和具體方案的改進(jìn)措施,節(jié)省了廠房投資成本,驗(yàn)證了未來的生產(chǎn)管理模式。